The evolution of a streetwise Siggi
11.12.2023
As many are aware, last summer we debuted our new folding bicycle which we named Siggi and presented her to the world on Indiegogo. Siggi is unique in many ways, being the first folding bike in the history of the world to be made of recyclable carbon fiber and sporting a dynamic combination of mini-velo techs such as lefty style front fork, Stainless steel baggage carrier, hydroelastic front & rear suspension, Adjustable steering geometry, Folding handlebars, disk brakes, an option for a Zehus electric motor with built-in battery and KERS, the possibility for a belt drive, 20” wheels and last but not least a profoundly sporty riding experience. Our first bikes were so inspiring that I chose to test one by riding it from Copenhagen to Vienna, Austria just to get to know it and understand what portions of the design would need to be developed before entering into production.
As one may guess, designing and building a new carbon fiber folding bicycle is in and of itself a considerable undertaking. To begin with, we needed to refine the frame geometry before committing to a final design because building mass-production tooling for composite frame manufacturing is a big investment, and very costly to alter once completed. We chose to manufacture production tooling from the start because that was the best way we could assess the design. Once we had a series of frames we needed to decide which configurations we were looking for. We quickly decided on an assortment of combinations that seemed to make sense: a traditional 11spd Chain drive, a Zehus e-bike, an Alfine internal gear configuration and the ability to fit a belt drive to the last of these two combinations.
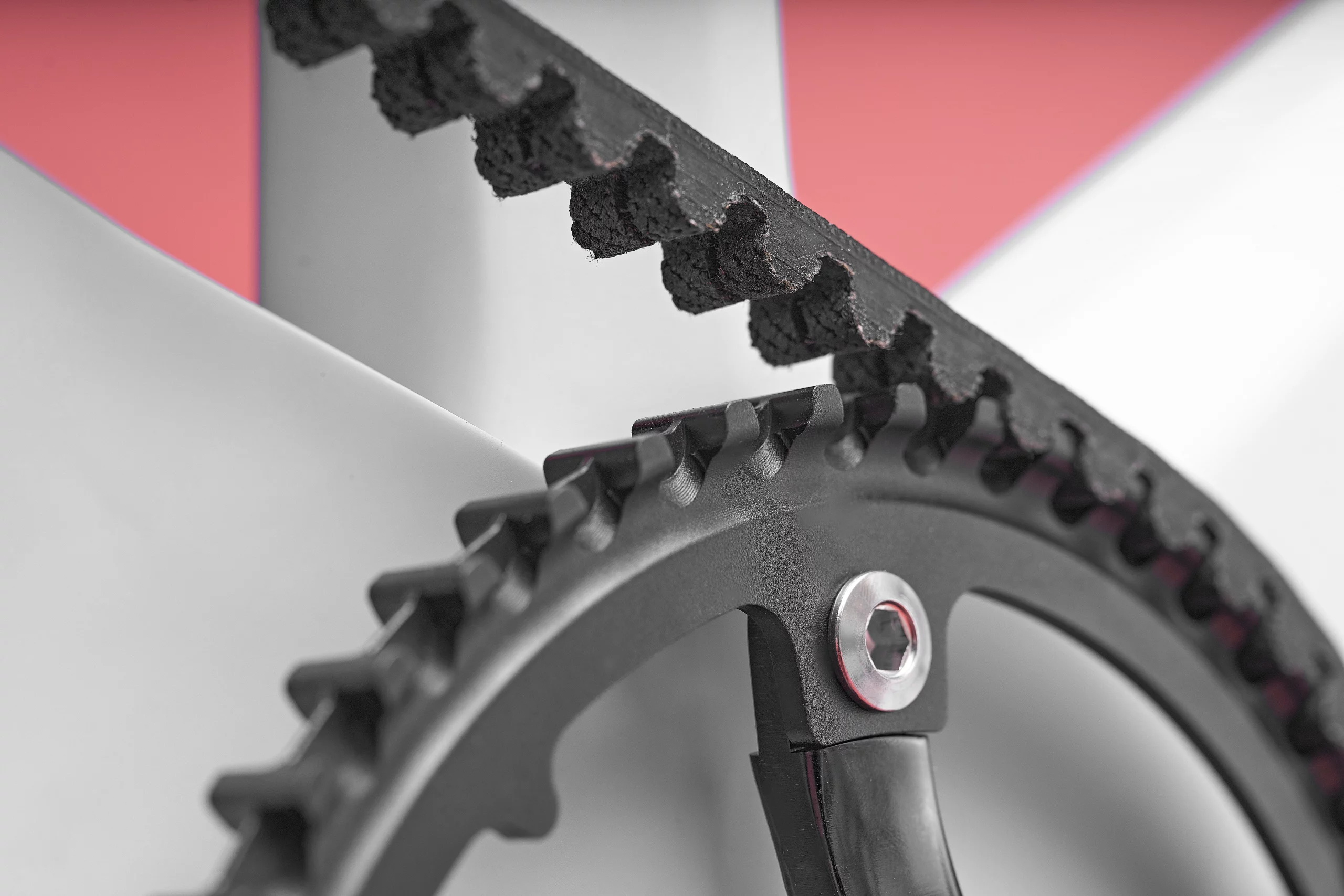
After deciding on configurations, it was important to focus on component design. Small-wheeled folding bicycles are unique; they are sort of a cross between a bicycle and the proverbial Swiss army knife. This means that although some standard components may fit many standard components may not fit or in the best case will require modifications. Now, since the first bikes, and the one I rode to Austria, were just fully functional prototypes, we needed to look at the component market and assess the compatibility, performance, availability, and economics of all of the approximately 282+ components that are needed to produce these bikes and their different configurations. Each part needed to be assessed and looked at from a manufacturing perspective to ensure repeatability, performance, and availability could fall in line with the resources available.
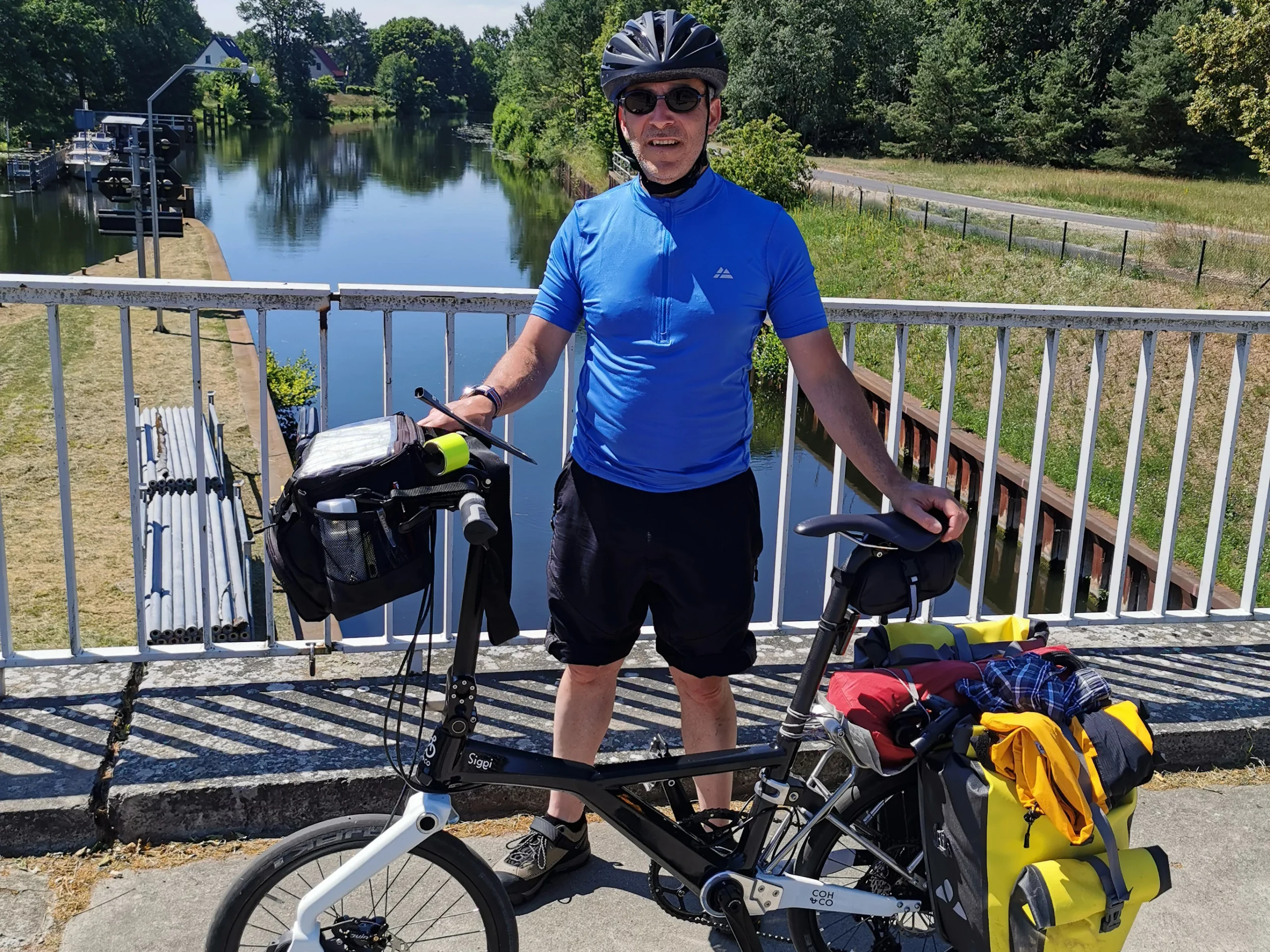
At this point, we have had 3 months of communicating with component manufacturers from all over the world and are excited to see the component package coming together – super lightweight hollow axel direct mount cranks with integrated chainguard, a great crew of custom component suppliers ranging from robot welding in Holland to CNC milling in Asia. Even our pedals have required going back to ground zero – we are patiently awaiting the production models of a new model inspired by our conversations with our pedal supplier at Eurobike 2022.
As our component list matures we have now turned our focus toward testing and as we speak we are punishing the daylights out of our single-sided fork assembly subjecting it to the European mountain bike fork test standard.
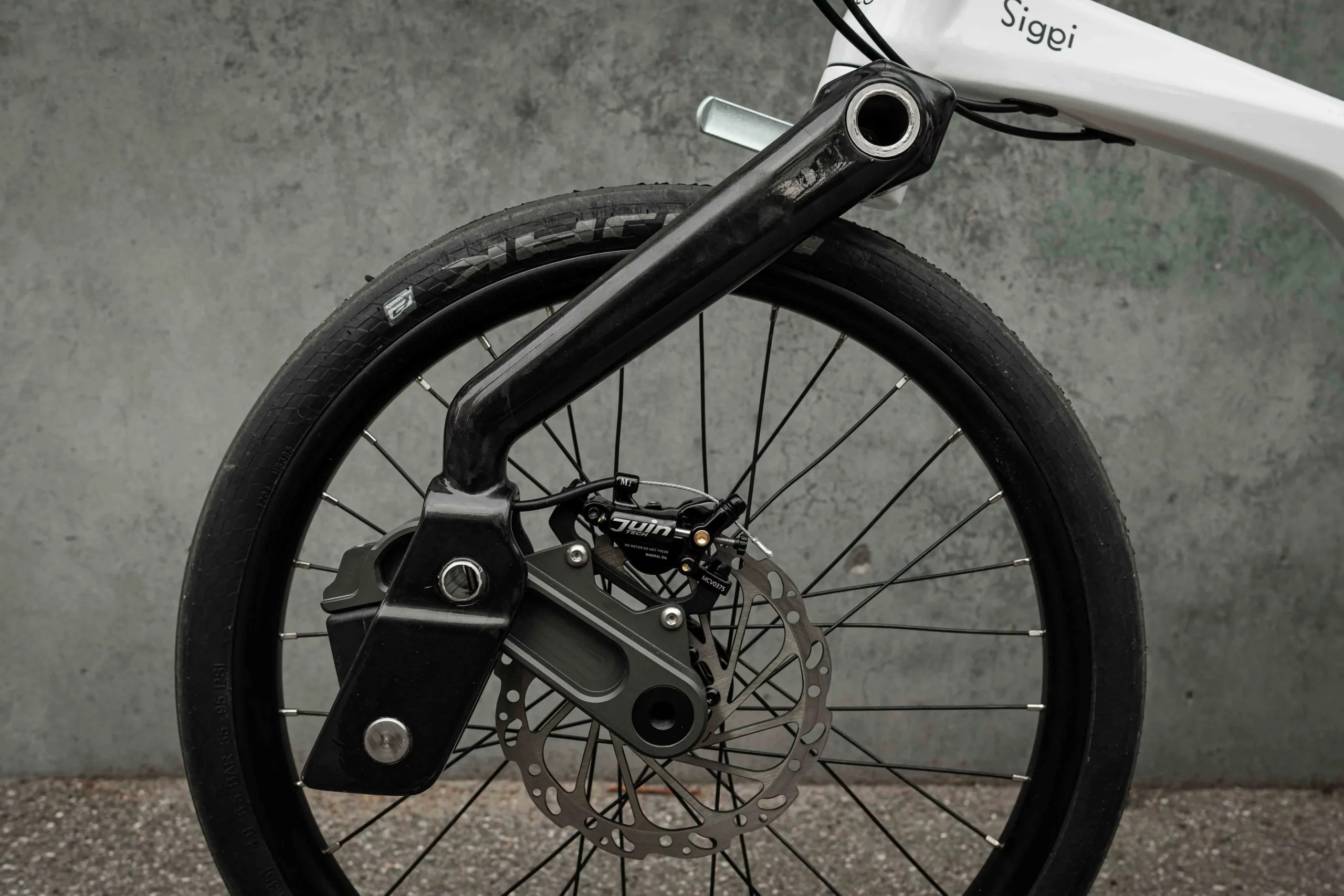
Siggi is coming together nicely and should be ready for assembly and shipping late in the first quarter of next year or early spring. I am beginning to dream of where I can take her next summer… Copenhagen to Milan?
Check out the Siggi campaign and get your very own Siggi by clicking the button below