Revisiting the roots of our classic proprietary dropout
27.11.2023
Here at Coh&Co, we are great fans of modularity. Our modular design journey began with the development of our dropouts and we believe that this approach has given us a unique opportunity to tune and service our models in a manner very unique to Coh&Co all while offering longer product life cycles and flexibility without having to sacrifice performance.
Originally designed for our WooCa frame technology we needed a dropout design that would do more than interface with a wheel and a chainstay. We also needed a system that would contain and support the wood and carbon fibers without imparting destructive loads onto the chainstay and seatstay. Composite fiber structures made of carbon fiber, basalt fiber and even wood (as was the case with our original wood and carbon frames) do not take well to any splitting forces imposed by a wedge or implant that could conceivably pry them apart and split the laminate.
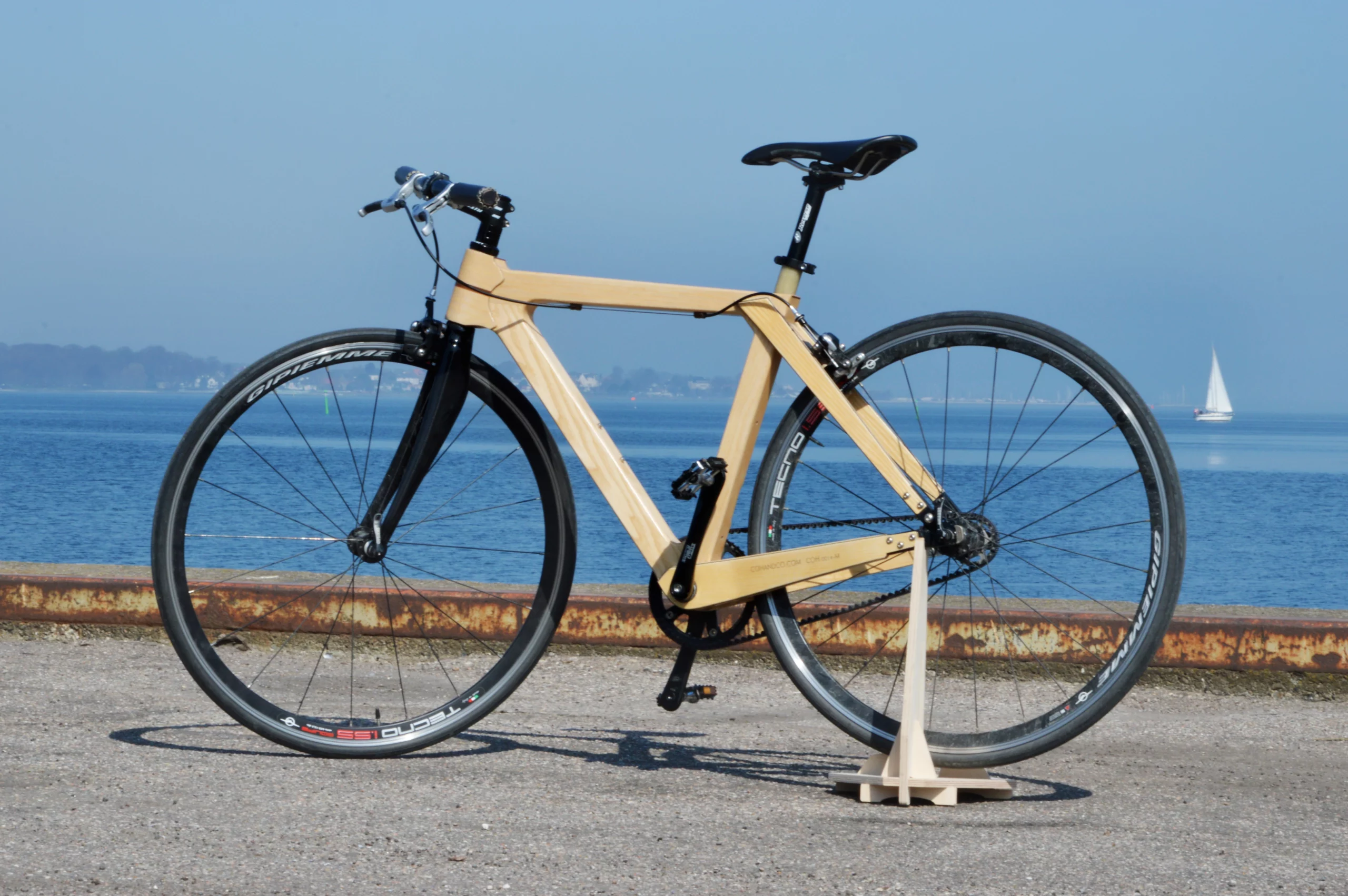
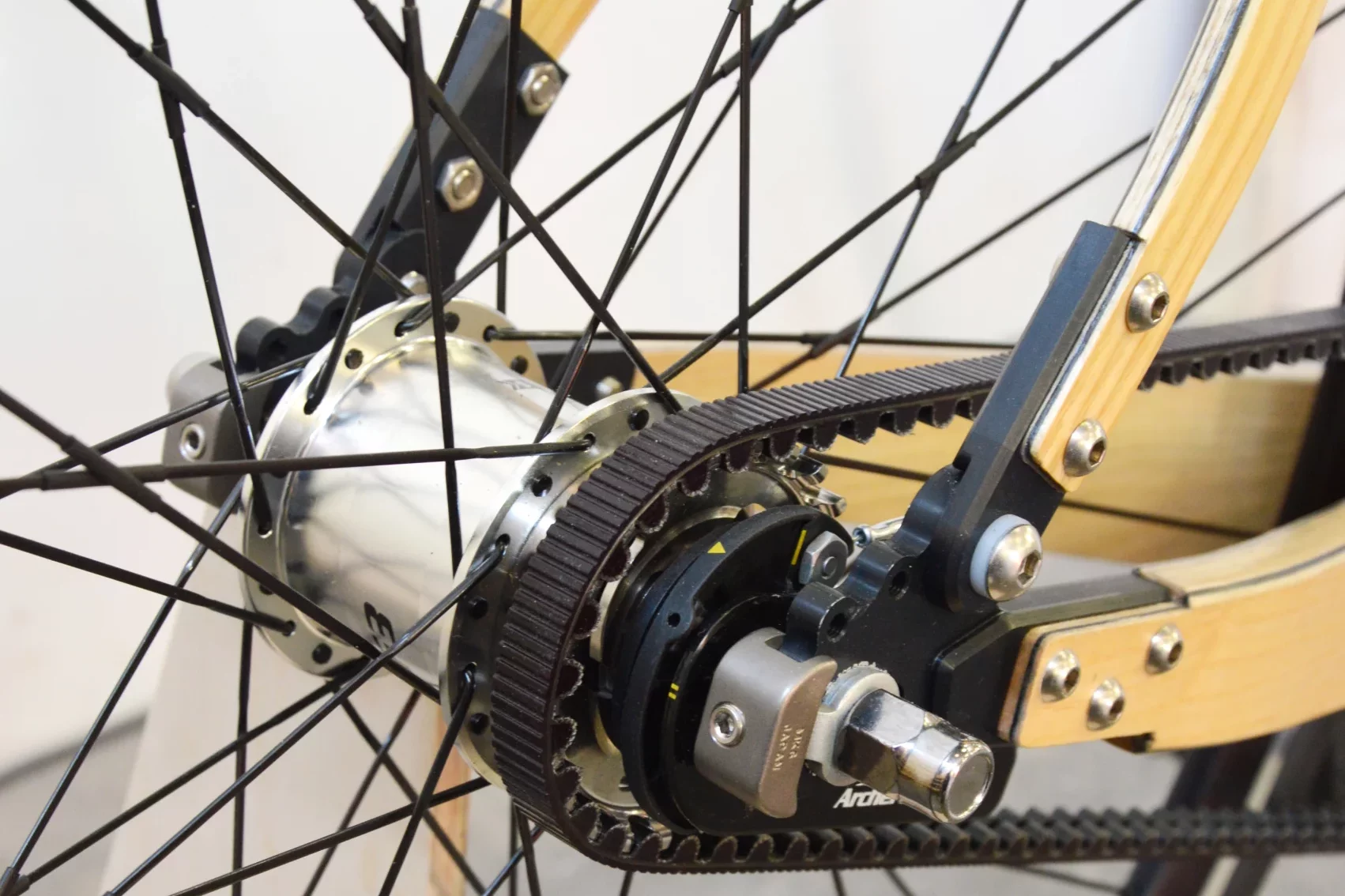
Our dropouts are a bonded fit that transfers all the force through the geometry of a joint – similar to how a dovetail joint works. Three fasteners are present to keep the part aligned and in place but they are not what is taking the riding load. This style of fastener provides a pretty optimal load transfer scenario for a mechanical style transition between the fibrous composite material of the frame and the mechanics of the drivetrain/wheel assembly.
In addition to providing a mechanically intuitive transition between mediums, these dropouts also allow us to take a single-frame design and adapt it to a variety of needs. Be it horizontal, trackstyle dropouts for tensioning a belt drive installation or a derailleur hanger or even adjusting the OLD from 135 to 142mm the design of the system assures that most versions are compatible with each other. Such a system allows us to define the specifics of a bike frame and its associated hardware composition at a later stage in the production life cycle thus allowing for a more flexible business model. Changes can even be made retrospectively.
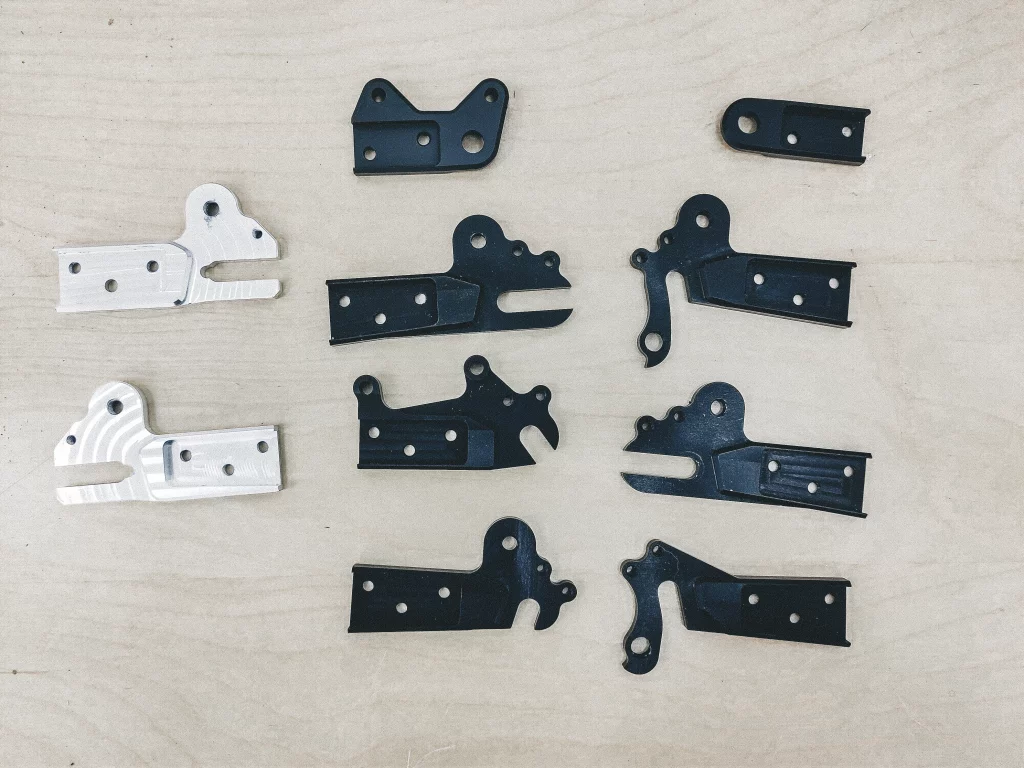
Selection of our proprietary dropouts
Finally, there is another great advantage of these style dropouts. Our frames are made of a combination of Carbon fiber, Basalt fiber and Epoxy and although these materials don’t corrode in and of themselves, the metals that come in contact with them do corrode and making this connection modular allows customers to service dropouts by switching them when and if they have corroded. In addition to maintenance, this also allows us to use a higher grade aluminum like EN 7075 on our dropouts without concern for corrosion because they can just be changed if there is an issue. Corrosion is very dependent on the environment and use, so wet salted roads all winter long will tear on a dropout connection whereas a dry summer climate will not be as likely to provoke corrosion.
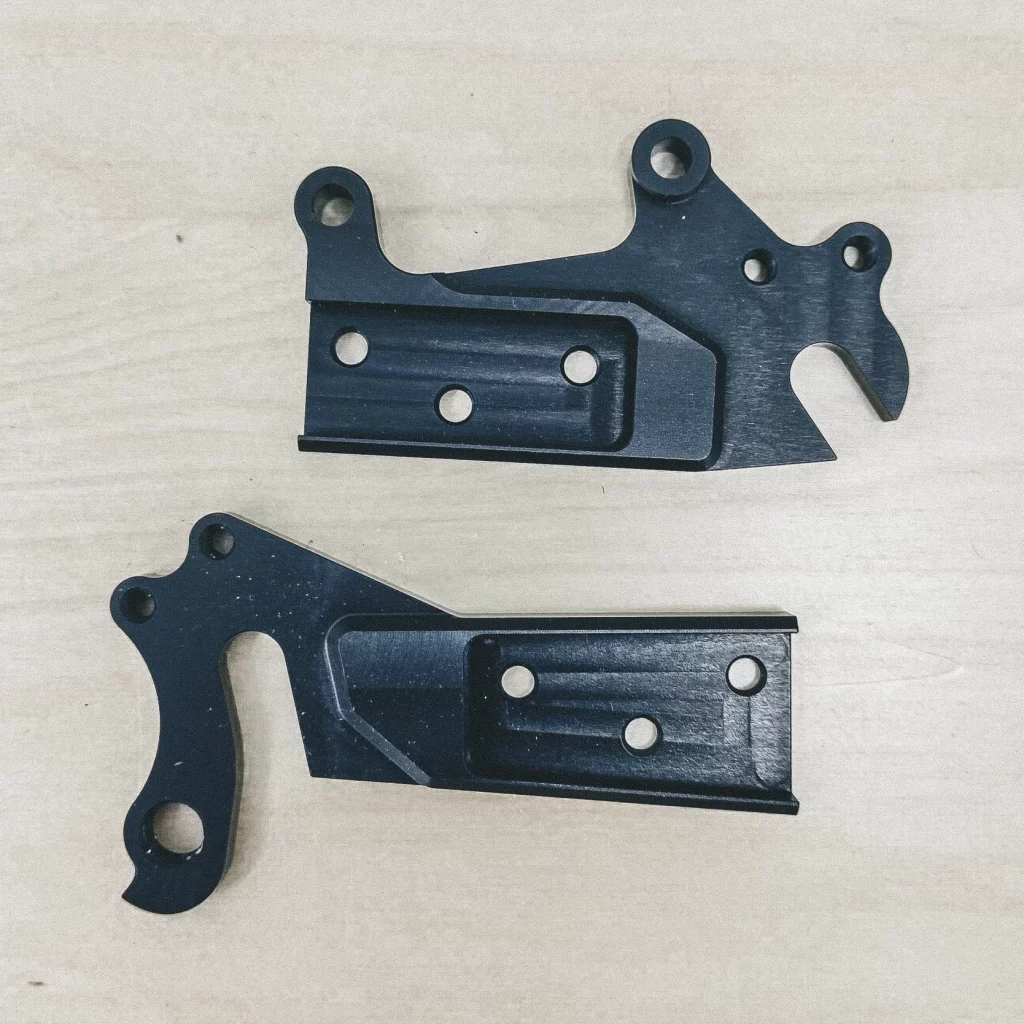
All of our dropouts are based on our same internal standard and it should be noted that, just like any other critical component on your bike, they must be inspected and maintained at regular intervals!
Check out this week’s Tuesday Deal and get your very own Erik Electric featuring Coh&Co’s modular dropouts. Learn more by clicking the button below